Textile
Textile is any material made of interlacing fibers, including animal fibers, plant fibers, and synthetic fibers. It is used to make a variety of products, including clothing, home furnishings, and industrial products. The history of textile production dates back to prehistoric times, when people first began to weave fibers into fabric. This process has been refined over the centuries, and today, textiles are produced in a variety of ways, including weaving, knitting, and felting.
In weaving, two sets of yarns are interlaced to form a fabric. The first set of yarns, the warp yarns, are placed on a loom and held in place. The second set, the weft yarns, are then passed over and under the warp yarns to form a pattern. Knitting is a process in which one set of yarns is looped around another set of yarns to form a fabric. The loops are formed by knitting needles that are used to manipulate the yarns. Felting is a process in which fibers are matted together by heat, moisture, and pressure. This process is used to create felt fabrics, which are often used in clothing and accessories.
Textiles are used to make a variety of products, including clothing, upholstery, carpets, and curtains. They are also used to create industrial products, such as filters, insulation, and rope. Textiles are also used in the medical field, to create bandages, sutures, and prosthetic devices. Textiles are produced from a variety of fibers, including natural fibers such as cotton, wool, and silk, and synthetic fibers such as polyester, nylon, and acrylic. Each type of fiber has different characteristics, and when combined with other fibers, can create fabrics with unique properties.
Vishnu Spinning
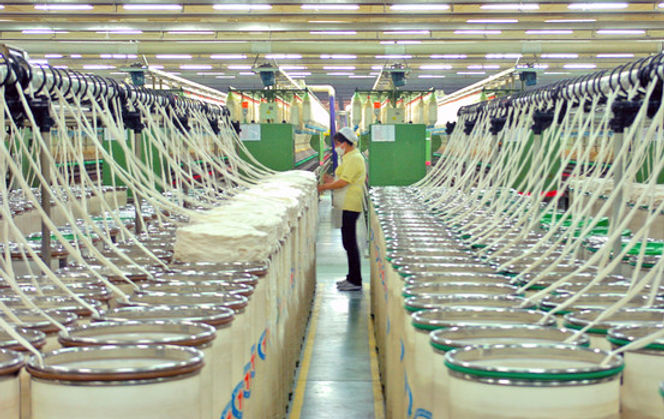

At a glance:
-
Vishnu is currently producing Hosiery Yarn and producing high-quality value-added Yarn for export. We are also producing Melange Yarn with different shade proportions as per the party’s requirement.
-
Our unit has a 32000 spindle capacity.
-
We produce an average of 29.5’s count with a production capacity of 11-12 Ton/ day
-
We have to produce 24’s 30’s and 34’s cotton single yarn and in Melange ’30s, 34’s,40’s,26’s, and 38’s yarn with differ blend variations as per parties' requirements.
-
We are certified with GOTS and OCS. GRS And ISO 9001
TYPE | MAKERS | NO. OF MACHINES |
---|---|---|
Yarn Board Appearance | Statex | 1 |
Electronic Twist Tester | Statex | 1 |
wrapping Block | Statex | 1 |
Neps Checking | Eureka | 1 |
Sherly Trash Analyser | Statex | 1 |
Lea strength tester | Statex | 1 |
Premire Uster | Premire | 1 |
EMPLOYEE | NUMBER |
---|---|
STAFF | 67 |
FEMALE WORKER | 62 |
MALE WORKER | 471 |
01
Machinery Details:
-
Blow Room – LMW 2 Lines
-
Carding – LMW 14 nos of LC-300, 02 nos of LC–300A & 02 nos of TRUZ DK - 800
-
Draw Frame – LMW Make 05 nos DO -6,
-
Finisher Frame-05 nos RSB 851.01 nos Rieter RSB-851
-
LAP Former – LMW Make 01 nos LH-10
-
Comber – LMW Make 02 nos LK-54, 06 nos LK- 250, 03 nos Reiter E7/5.
-
Simplex – LMW Make –08 L/R 1400 A.
-
Ring Frame – LMW Make – 21 nos G5/1, 04 nos L/R-6, 07 nos L/R- 65.
03
Utilities:
-
Transformer Capacity – 1 nos - 2000 KVA & another 1 nos – 1500 KVA
-
Air Consumption – 700 CFM
-
Water Consumption – 50000 litter per day
-
Solar Energy - 10% of required energy
02
Finishing:
Finishing:
-
Auto Corner – 07 nos Savio, 02 nos SCHLAFHORST – X5, 01 nos SCHLAFHORST – X6. Muratec QPRO=01
-
Yarn Conditioning – Singer .
Value Added Service (Twisting):
T.F.O – 02 nos VJ- 15 H.
04
Products:
-
Ring Spin Yarn
-
100% Cotton Carded and Combed Yarn Ne 20/1-40/1
-
Melange Yarn Ne 20/1-40/1 (Blended as per requirements)
-
Blended Yarn (100% Cotton), Cotton – Polyester, Cotton – Viscose and Dyed Yarn Ne 20/1-40/1’s
-
Slub Yarn
Knitting


At a glance:
With a capacity of processing 35,000 kilos of fabrics
per day, our wide range of knitting machines
produce aweless materials of single jersey, pique, Lycra
fleece, interlock, auto stripe with lycra, rib with lycra and many more; all undergoing a strict quality inspection before advancing to the next steps.
Transformer Capacity: 650 KVA ( Knitting )
Air Consumption: 800 CFM ( Knitting )
Water Consumption (Per Day): 1250Lit. (Knitting)
TYPE | MAKER | NO. OF MACHINES |
---|---|---|
Lab weight machine | YKW | 1 |
Yarn fabric Moisture Checking | Delmhorst (USA) | 1 |
Yarn Tension Tester Digital | Schmidt ( Germany) | 1 |
Fabric UV Checking | Local | 2 |
Fabric inspection table | RAM DUKES | 1 |
Fabric inspection table | UZU | 3 |
Total No of Machine: 77 nos.
-
Pilong: 60 nos.
-
Mayer – 14 nos.
-
Terrot – 03 nos.
Production per day : -
85% efficiency,
-
27 ton per day.
Manpower: -
Male Worker= 134
-
Female Worker=3
-
Staff= 38
Fabric checking machine: 04 nos.
Gauge:
-
18
-
24
-
28
-
32
Products:
Single Jersey
-
Gauge: 24, 28, 32
-
Diameter: 30, 34 inch
Interlock/ Double Knit
-
Gauge: 18,24, 28,32
-
Diameter: 34
Rib- Single & Double
-
Gauge: 18
-
Diameter 34
Fleece 2/3 Thread
-
Gauge: 24
-
Diameter: 34
French Terry
-
Gauge: 20
-
Diameter: 34
Lycra Fabrics
Dyeing


Boiler: Thermax Rice Husk Fired (The rice husk have substantial potential for the production of power and energy. The energy obtained from this process is renewable energy which is considered environment-friendly. Using this technology, the timber and coal used as fuel in the power plants can also be saved from its depletion)
Our advanced dyeing facilities ensure the most vibrant and accurate set of colours, double-checked for colorfastness. We pride ourselves on using AZO-free colures to protect our stakeholder from preventing any hazardous situation. Our dyeing facility has a capacity of 40 tons per day with ‘High-Temperature Specialized Dyeing Machines’ and ‘Sophisticated Soft Flow Machines’ for colouring CVC, Lycra, PC and Polyester etc.
DEPARTMENT | Machinery |
---|---|
Open Compactor | Ferrarao (Italy)=02 |
Stenter | Bruckner (Germany)=01 |
Slitter | Bianco (Italy)=02 |
Compactor | Ferrarao (Italy)=02 ; Santex(Switzerland)=01, Ferrarao(Italy)=03 ; |
Dryer | Santex ( Switzerland)=02, Bruckner(Germany)=01, Fong’s(China)=01 |
Padding/ Squeezer | Bianco (Italy) =03 ; Santex ( Switzerland)=01 |
Dyeing | Brazzoli (Italy) =02 No. ; Sclavos ( Switzerland)=03 ; Thies (Germany)=06; Fong ( China)=15 |
TYPE | MAKER | NO. OF MACHINES |
---|---|---|
Washing Machine | Samsung | 1 |
Auto Dryer | Bosch(Germany) | 1 |
Infrared Dyeing Machine | RBE | 2 |
Fabric Dyeing Machine Details:
Quality control
01
Manpower:
-
Male Worker= 218
-
Female Worker= 60
-
Staff= 25
03
Statistics
Transformer Capacity: 650KVA
Air Consumption: 450 CFM
Water Consumption (Per Day): 14 Lakh lit
Steam Consumption (Per Day): 80 Ton
02
Production per day :
-
27 ton per day.
04
Effluent treatment plant(ETP):
10 Lakh Litter /Day
YARN DYEING & SEWING THREAD
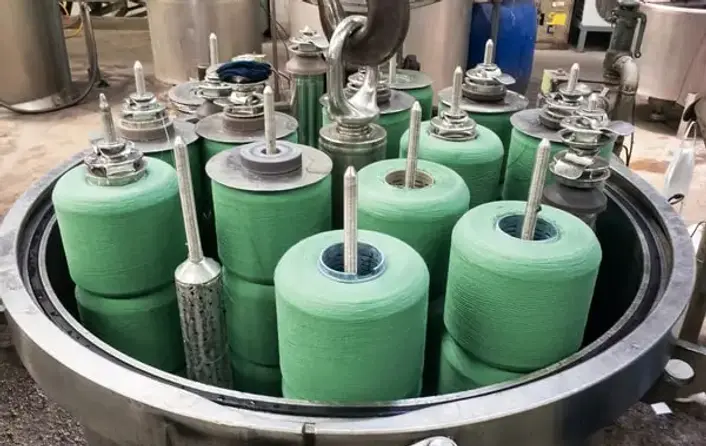

Yarn dyeing is a process used in textile production that involves dyeing the yarn itself before it is woven or knitted. This is in contrast to piece dyeing, which is done after a piece of fabric or garment is already constructed. Yarn dyeing is an important part of textile production, as it creates a more consistent and vibrant color in the finished product.
Yarn dyeing can be done in a variety of ways, depending on the type of yarn and the desired final product. For instance, a yarn may be dyed in a solid color or a combination of colors. It can also be dyed in a pattern or with a gradient of colors.
The yarn dyeing process typically begins with the yarn being washed and then soaked in a dye bath. Depending on the type of dye used, the yarn may need to be heated or exposed to chemicals to help the dye penetrate the fibers. Once the yarn has been dyed, it is rinsed and dried before being used in production.
Yarn dyeing is an important part of textile production, as it helps maximize the color and visual appeal of the finished product. It also allows manufacturers to create unique and vibrant colors and patterns that can be used to differentiate their products from competitors.

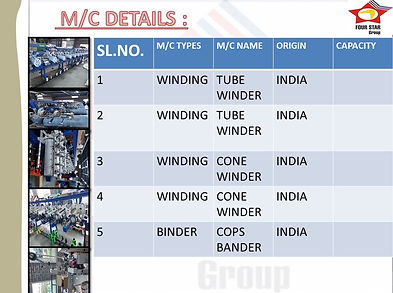

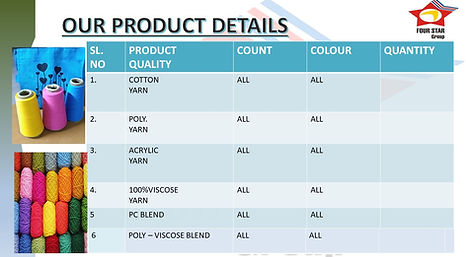
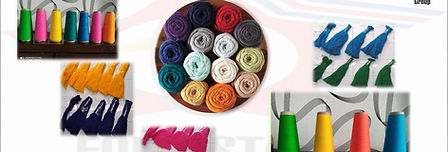
Weaving
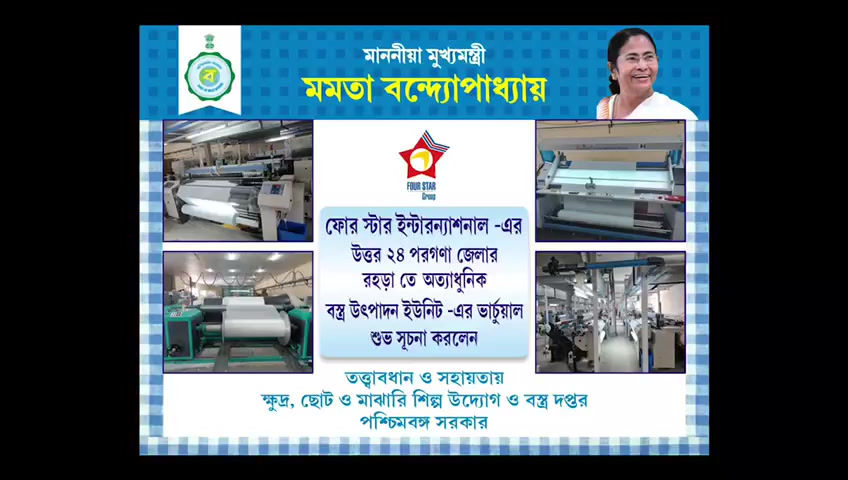
Weaving is a textile production technique that involves interlacing two sets of yarn or threads at right angles to create a fabric or cloth. The threads used in weaving can be made from a variety of natural and synthetic fibers, including cotton, wool, silk, and synthetics such as nylon and polyester. Weaving is one of the oldest textile production techniques, dating back to ancient Egypt, and is still widely used today in the production of clothing, home furnishings, and other textile products.
Weaving involves several steps. First, the individual threads are wound onto a loom, which serves as the foundation for the weaving process. The warp threads are stretched directly across the width of the loom, and the weft threads are then passed over and under the warp threads to create the weave. The loom holds the threads in place, allowing weavers to create intricate patterns and designs. The type of weave used depends on the desired product—the plain weave is typically used for everyday fabrics, twill weave is often used for heavier fabrics, and the jacquard weave is often used for decorative fabrics.
Weaving is an essential part of the textile industry and has evolved significantly throughout the years. New weaving techniques and technologies have made it possible to create fabrics of various colors, textures, and patterns. Weaving is an important part of the fashion industry, and fabrics produced through weaving are used for everything from clothing to home furnishings.

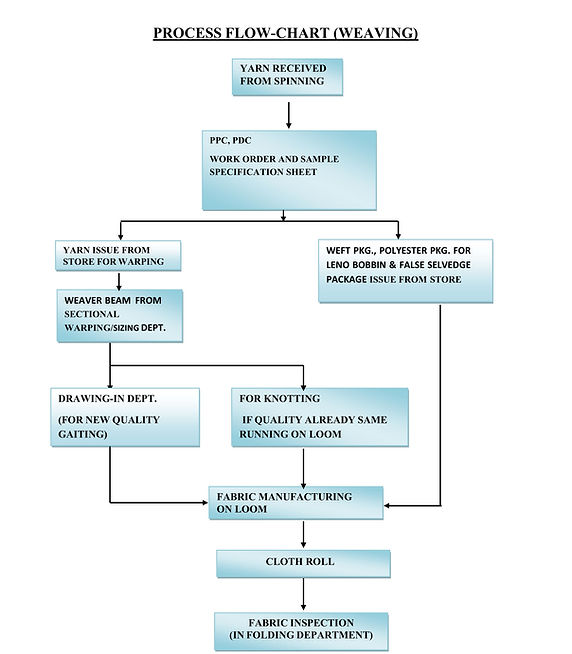